Guide To Surface Mount Technology
Surface Mount Technology is a method that allows electronic components to be pasted and soldered directly onto the surface of circuit boards using automated production lines. Unlike Through-Hole Technology, SMT enables components to be mounted on both sides of a circuit board, eliminating the need for drilling holes.
This approach not only saves space but also increases the density of components, making it ideal for compact devices such as smartphones and medical equipment.
What is Surface Mount Technology?
Surface Mount Technology is a method that allows electronic components to be pasted and soldered directly onto the surface of circuit boards using automated production lines. Unlike Through-Hole Technology, SMT enables components to be mounted on both sides of a circuit board, eliminating the need for drilling holes.
This approach not only saves space but also increases the density of components, making it ideal for compact devices such as smartphones and medical equipment.
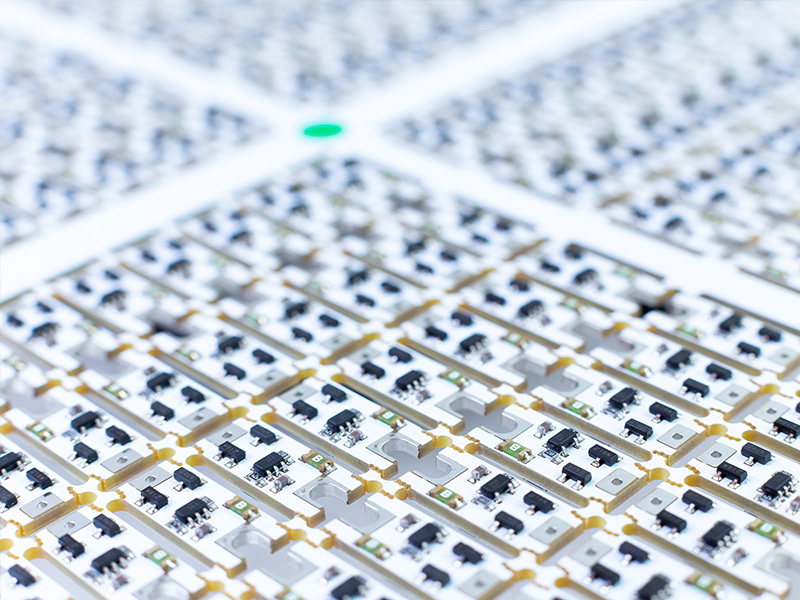
Benefits of Surface Mount Technology
SMT has been a revolutionary advancement in modern electronics. It allows for a higher number of components to be placed on smaller boards, enables quicker production times, and keeps costs down while ensuring reliability.
Benefit #1: Higher Component Density
The automation of the Surface Mount Technology process means a greater density of component mounting can be achieved – i.e. a large number of components and connections per component can be placed on small circuit boards. This allows for much greater efficiency within the manufacturing process of much smaller PCBs.
A much higher density of connections on the circuit boards is possible because there are no holes to block the routing space. As more components can be closer together on the circuit board, the PCB design can be much more lightweight and compact.
SMT electronics assembly allows for the manufacture of products with ever smaller dimensions. As such, very small and sensitive components, such as resistors and diodes, can be quickly and effectively mounted on circuit boards.
SMT is a perfect technique for complex and unique assembly requirements. In addition, it is also highly customisable and comes with the power and flexibility to meet these types of PCB assembly demands.
Benefit #2: Cost Savings Through Surface Mount Technology
One of the greatest benefits of using Surface Mount Technology is the cost savings which can be made at all stages of the manufacturing process, when used as an alternative to Through Hole Assembly. These include:
Lower initial cost and set-up time for mass production
Faster automated assembly leads to reduced production time
Greater uniformity in component soldering means less room for error
Many SMT parts cost less than through hole parts
Reduced labour costs
Additional Benefits of Surface Mount Technology
Take a look below at a list of the additional benefits associated with the use of surface mount technology:
Easy manufacture of ever-smaller, lighter and more powerful PCBs
Faster assembly rate than through hole insertion
Well suited to complex and unique PCB assembly requirements
Reduction of mechanical heat and noise
Ability to place more components more closely together, enabling smaller, lighter and more powerful circuit boards
Greater reliability
The Surface Mount Technology Process
The SMT assembly process, which is used by the electronics experts at MPE, follows this method:
1. Solder Paste Application
Solder paste is applied on the board through a solder paste printer, using a template (also known as a stencil or solder screen) to ensure it is accurately applied to those places where components will be mounted. An inspection will pick up any defects and the printing reworked or the solder paste washed off prior to second printing.
2. Component Placement & Mounting
The PCB is then sent to the pick-and-place machine where all the electronic components are mounted on to their corresponding pads via component reels, tubes and waffle trays in the machine.
3. Reflow Soldering
Once all the components are in place the board goes through reflow soldering, passing through a furnace, causing the solder paste to liquefy and bind the SMD components to the board.
4. Quality Inspection
Our machines will check that the part used in the assembly process matches its specification and, when the PCB is populated, high speed Automatic Optical Inspection (AOI) machines can verify that the part fitted to the PCB is in the right place and matches not only the specification but is also soldered correctly.
Talk To Us About Your PCB Assembly Requirements
At MPE Electronics, we take product quality very seriously, using the latest equipment and systems to make sure PCB assemblies meet client specifications.
Contact us now on 01825 764822 or email enquiries@mpe-electronics.co.uk to find out more about how Surface Mount Technology could benefit you.
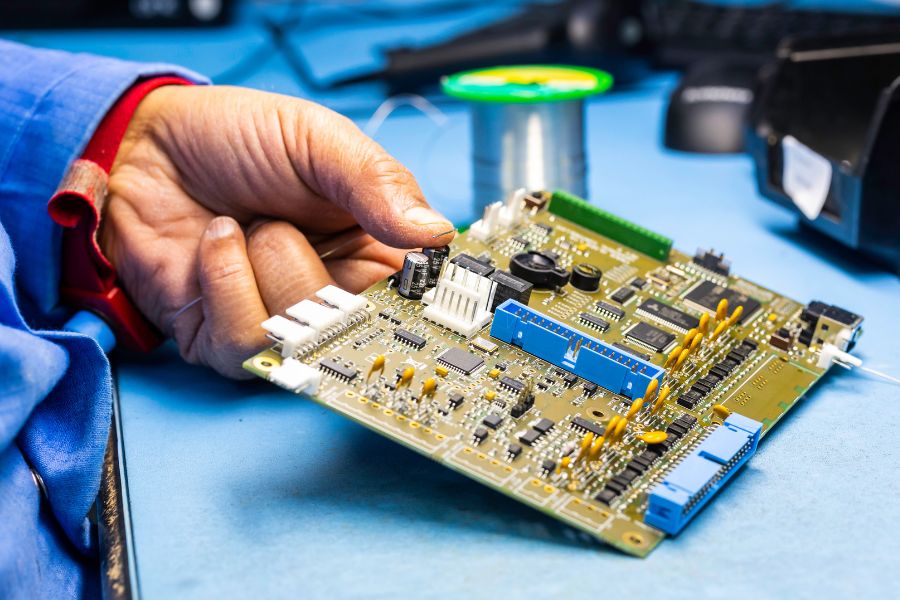
PCB Assembly
Precise, reliable PCB assembly to your exact requirements.
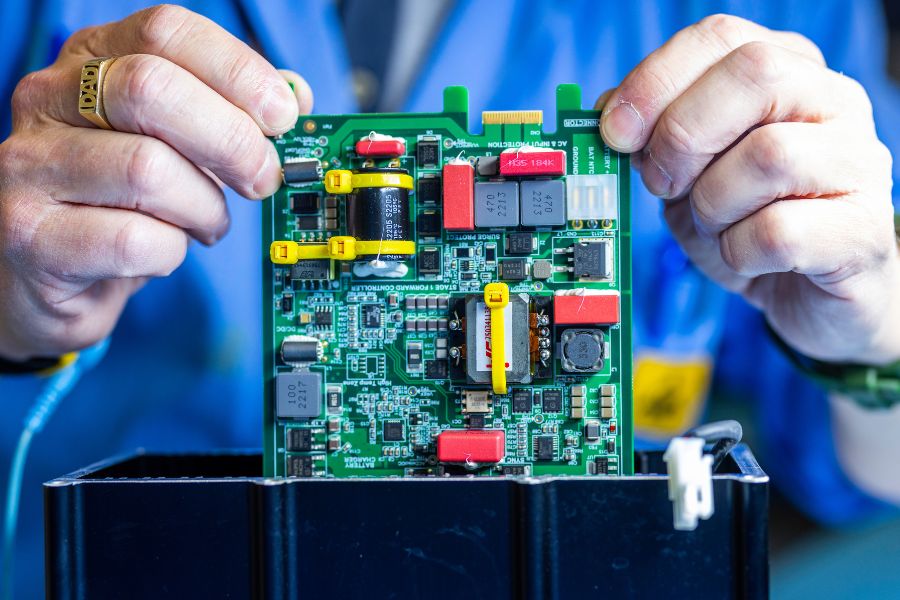
Box Build Assembly
Optimise your supply chain with our turnkey assembly service.